The lighting industry has always embraced innovation, constantly striving to push the boundaries of design, efficiency, and durability. One such groundbreaking advancement that is revolutionizing the landscape of lighting is neon strip co-extrusion manufacturing. This cutting-edge manufacturing process combines the classic appeal of neon lighting with modern technology, resulting in a myriad of advantages that are redefining the industry. In this article, we will explore the plethora of benefits that neon strip co-extrusion manufacturing brings to the table, solidifying its role as the future of lighting design.
Enhanced Durability and Longevity:
Neon strip co-extrusion manufacturing introduces unprecedented durability and longevity to neon lighting. By employing a co-extrusion process, neon strips are endowed with a robust outer layer that is very durable but flexible, offering protection against external factors such as physical impact, UV radiation, moisture, and temperature fluctuations. This enhanced durability translates to a significantly extended lifespan, making it an ideal choice for residential, building facade, yacht, and commercial lighting applications.
Versatility and Design Flexibility:
One of the key advantages of neon strip co-extrusion manufacturing is its versatility and design flexibility. This manufacturing process allows for the creation of neon strips in a wide range of colors, shapes, and sizes, catering to diverse lighting needs and design preferences. Whether creating intricate signage, captivating architectural lighting, or eye-catching displays, designers can now seamlessly integrate neon strips into various applications with ease. Additionally, the flexibility of neon strips ensures they can be curved, twisted, and shaped to suit even the most complex installations, offering unparalleled design possibilities.
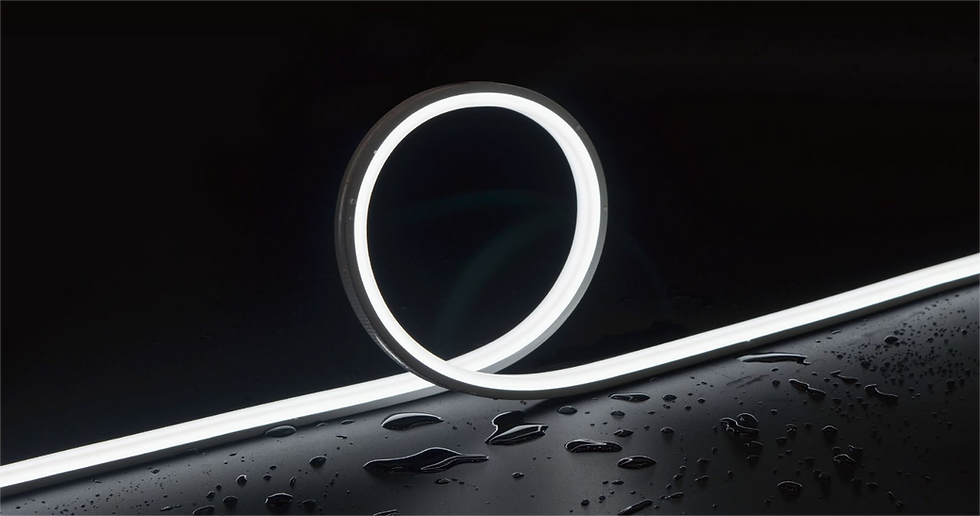
Flexible
Energy Efficiency and Cost Savings:
Neon strip co-extrusion manufacturing embraces the energy-efficient marvel of LED technology. By incorporating LEDs within the neon strips, this manufacturing process reduces energy consumption while maintaining the luminous appeal of neon lighting. With reduced energy requirements, both residential and commercial users can enjoy substantial cost savings on their energy bills without compromising on aesthetics or brightness. Neon strip co-extrusion manufacturing aligns sustainability with economic advantage, making it an attractive choice for environmentally conscious individuals and businesses alike.
Easy Installation and Maintenance:
Gone are the days of complex installation processes and fragile components. Neon strip co-extrusion manufacturing simplifies installation and maintenance, making it accessible to both professionals and DIY enthusiasts. With its flexible nature and assembling end cap design, neon strips can be easily installed on various surfaces or recessed, ensuring a hassle-free experience. Furthermore, the absence of glass tubes and the diffuser greatly reduces the need for regular maintenance, providing peace of mind for users.
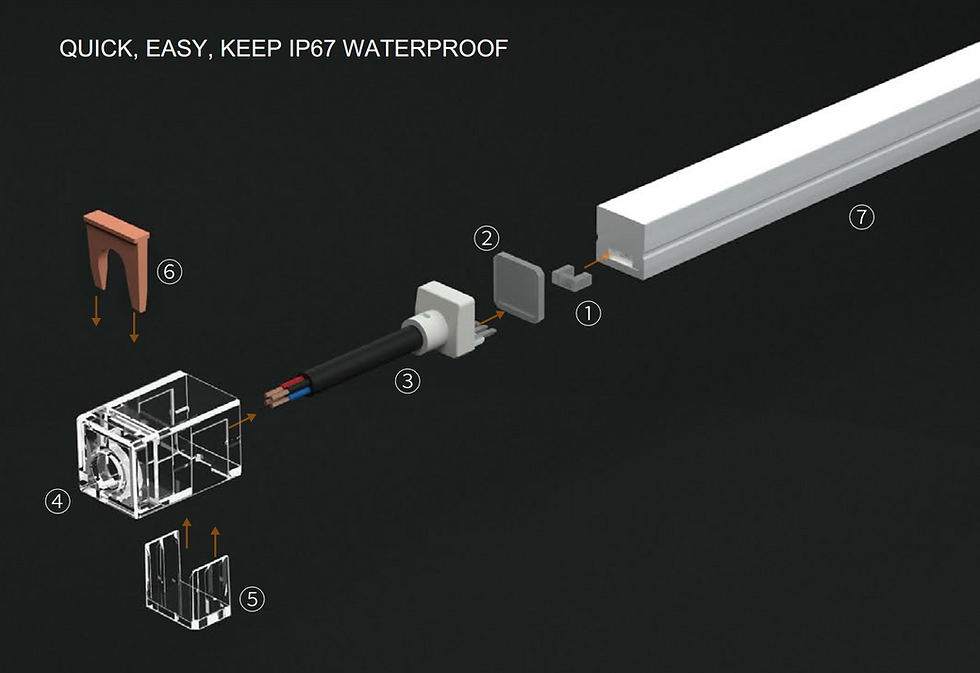
Assembling End Cap
Environmental Considerations:
Neon strip co-extrusion manufacturing places a strong emphasis on environmental sustainability. By utilizing LED technology, this manufacturing process significantly reduces energy consumption compared to traditional neon lighting, aligning with global efforts to minimize carbon footprint. With no harmful substances like mercury present in neon strip co-extrusion manufacturing, it emerges as an eco-friendly choice that respects both nature and the health of individuals.
Conclusion:
As the lighting industry continues to embrace innovation, neon strip co-extrusion manufacturing emerges as a trailblazer, transforming the landscape of lighting design. With enhanced durability and longevity, versatility and design flexibility, energy efficiency, and cost savings, easy installation and maintenance, and environmental considerations, this groundbreaking manufacturing process offers unparalleled advantages that have immense potential to shape the future of lighting. As we embrace the era of neon strip co-extrusion, we can envision a world where captivating linear lighting experiences coexist harmoniously with sustainability, bringing to life spaces that seamlessly blend functionality and aesthetics.

Project